Автор: ГалинаРаздел: Анализ микроструктуры материалов
Автор: ГалинаРаздел: Анализ микроструктуры материалов
Автор: Раздел: Атомно-силовая микроскопия
Автор: ГалинаРаздел: Анализ микроструктуры материалов
Автор: ВикторРаздел: Атомно-силовая микроскопия
Автор: ВикторРаздел: Атомно-силовая микроскопия
Автор: ВикторРаздел: Атомно-силовая микроскопия
Автор: ГалинаРаздел: Анализ микроструктуры материалов
Автор: ГалинаРаздел: Анализ микроструктуры материалов
Автор: ВикторРаздел: Анализ микроструктуры материалов
Нажимая кнопку «Подписаться», вы принимаете условия «Соглашения на обработку персональных данных».
Распознавание дефектов на слое покрытия с использованием наномеханического режима PinPoint атомно-силовой микроскопии
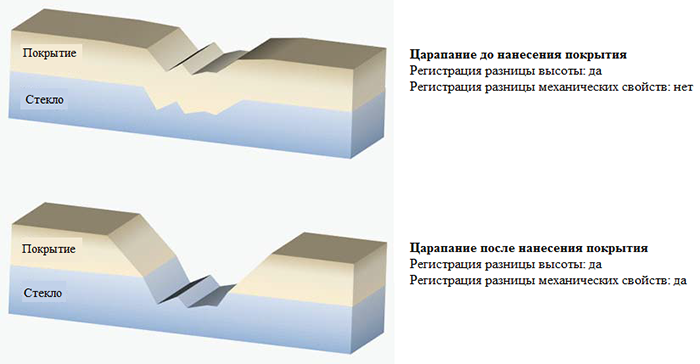
Обработка поверхности является критически важным этапом в различных областях и отраслях, таких как автомобилестроение [1], авиакосмическая промышленность [2], строительные материалы [3], а также мобильные и прецизионные устройства [4]. Методы обработки покрытия поверхности обычно включают процесс нанесения покрытия, который широко используется в промышленности для предотвращения истирания поверхности и коррозии. В последнее время была разработана возможность придавать материалам для покрытия специальные свойства, такие как антистатичность [5], антибактериальность [6] и защита от электромагнитных волн [7]. Популярность цифровых устройств значительно возросла в течение 1990-х годов; эта популярность привела к быстрому развитию технологий промышленного нанесения покрытия. Данные технологии усовершенствовали защиту устройств несколькими способами, включая защиту от царапин, защиту от отпечатков пальцев, химическую стойкость и защиту от ультрафиолетового излучения [8]. Атомно-силовая микроскопия (АСМ), широко используемая в области исследования поверхности материалов, также широко применяется для анализа покрытий [9]. Из анализа АСМ изображений толщина покрытия может быть получена из топографии поверхности образца, в то время как шероховатость поверхности дает информацию об однородности покрытия после нанесения. АСМ изображения позволяют производить контроль качества на возможные дефекты. АСМ измеряет как топографию поверхности, так и механические свойства. Используя дистанционно-силовые кривые на поверхности с покрытием, можно измерить такие механические свойства, как жесткость, энергия адгезии и модуль упругости [10].
В данной статье представлен новейший метод, разработанный компанией Park Systems под названием «Наномеханический режим PinPoint™», который позволяет исследовать механические свойства поверхности. Кроме того, здесь описывается, как этот метод можно использовать для анализа этапов, на которых возникают дефекты во время обработки поверхности материала, особенно в процессе нанесения покрытия.
Как правило, дефекты на поверхности образца можно наблюдать с помощью АСМ изображений. Тем не менее, трудно определить, когда именно дефект возник (во время какого этапа производства), наблюдая исключительно за топографией поверхности. Наномеханический режим PinPoint решает эту проблему: он собирает информацию о механических свойствах покрытой поверхности и позволяет определить, были ли дефекты созданы до или после нанесения покрытия.
Материалы и методы
Наномеханический режим PinPoint
Наномеханический режим PinPoint собирает топографические данные высокого разрешения, одновременно получая данные «сила-расстояние» для каждой точки из области сканирования [11]. Это позволяет измерять топографию поверхности образца, одновременно получая количественные данные о наномеханических свойствах, включая модуль упругости, энергию адгезии, степень деформации, жесткость и рассеяние энергии.
Экспериментальная установка
Для измерения механических свойств образца был использован наномеханический режим PinPoint на атомно-силовом микроскопе Park NX10 компании Park Systems в сочетании с кантилевером модели NSC36 (компания MikroMasch). Резонансная частота (f = 130 кГц) и коэффициент жесткости (k = 2 Н/м) кантилевера обеспечивают требуемую деформацию образца при сохранении достаточного прогиба кантилевера. Результаты были проанализированы с использованием программного обеспечения для обработки данных Park XEI, которое предоставляет количественные данные из изображений, сравнение значений механических свойств и характеристики материала поверхности.
Тестирование образцов
Для проверки способности наномеханического режима PinPoint распознавать дефекты, возникающие до и после нанесения покрытия, образцы были подготовлены двумя способами. Первый тест включал в себя создание царапины на поверхности стеклянной подложки с покрытием. Во втором испытании использовалась поцарапанная стеклянная подложка, на поверхность которой впоследствии было нанесено покрытие. Разница между временем создания дефекта может быть определена по тому, проявляется ли стеклянный материал на изображении при анализе царапины. Если царапина была создана до нанесения покрытия, стекло не будет отображаться, так как покрытие наносится поверх царапины. Если царапина была создана после нанесения покрытия, покрытие отслаивается и обнажает стеклянный материал. Дело в том, что при визуализации участка с использованием наномеханического режима PinPoint механические свойства поверхности (такие как сила адгезии и модуль упругости) показывают четкий контраст, когда кантилевер АСМ исследует различные материалы (стекло и покрытие). Эта информация не может быть определена только из топографии, что четко отображает рис. 1.
Рис. 1. Иллюстрация дефекта, созданного до и после нанесения покрытия. Разницу между материалами можно увидеть не только по глубине царапины, но и по механическим свойствам материала.
Результаты и обсуждения
Изображения топографии, энергии адгезии и модуля упругости двух образцов с дефектами, созданными до и после нанесения покрытия, были получены с использованием наномеханического режима PinPoint. Топографические изображения в обоих случаях подтвердили наличие царапины (см. рис. 2а и 3а). Изображения из этой области подчеркивают различия механических свойств между областью царапины и незатронутой областью.
Изучая изображения энергии адгезии и модуля упругости царапины перед нанесением покрытия (см. рис. 2b и 2c) выявлено, что они не показывают видимых различий в механических свойствах между участками царапины и покрытием. Рисунки 3b и 3c, где стеклянная подложка царапается после нанесения покрытия, показывают очень четкий контраст между царапиной и прилегающей поверхностью. Сравнение средней энергии адгезии и значений модуля упругости поверхностей до и после нанесения царапин позволяет четко различать две разные поверхности.
Рис. 2. Изображения стеклянной подложки, полученные с помощью наномеханического режима PinPoint, когда царапина была создана до нанесения покрытия. В полученных изображениях не наблюдается никакого контраста между покрытой областью и поцарапанной областью, как по энергии адгезии, так и по модулю упругости.
Рис. 3. Изображения стеклянной подложки, полученные с помощью наномеханического режима PinPoint, когда царапина была создана после нанесения покрытия. В полученных изображениях хорошо наблюдается контраста между покрытой областью и поцарапанной областью, как по энергии адгезии, так и по модулю упругости.
Используя программное обеспечение для обработки данных Park XEI, можно выбрать разные интересующие области одного и того же изображения, то есть область царапины и область покрытия (см. рис. 4). Для каждой области было рассчитано среднее значение энергии адгезии и модуля упругости: эти значения приведены в таблице 1.
На рисунке 4a показана выбранная область с покрытием, для которой рассчитанное среднее значение энергии адгезии составило 1.22 фДж. На рисунке 4b, область с покрытием и вскрытая стеклянная подложка были проанализированы отдельно. Значение энергии адгезии покрытия (1.15 фДж) совпадало с предыдущим значением, в то время как энергия адгезии стеклянной подложки демонстрировала более высокое значение (2.47 фДж). Кроме того, при сравнении значений модуля упругости области с покрытием (см. рис. 4c и 4d), полученные значения в 3.15 ГПа и 3.08 ГПа соответствовали друг другу. В противоположность значениям энергии адгезии, модуль упругости поцарапанной вскрытой стеклянной подложки показал более низкое значение в 1.79 ГПа.
Рис. 4. Выбор различных интересующих областей одного и того же изображения с помощью программного обеспечения Park XEI для вычисления средних значений адгезии и упругости по каждой области.
Таблица 1: Рассчитанные средние значения энергии адгезии и модуля упругости.
Энергия адгезии | Модуль упругости | |||||
Царапание | До | После | До | После | ||
Рисунок | 4a (вся область) | 4b (красная область) | 4b (зеленая область) | 4c (вся область) | 4d (красная область) | 4d (зеленая область) |
Среднее значение | 1.22 фДж | 1.15 фДж | 2.47 фДж | 3.15 ГПа | 3.08 ГПа | 1.79 ГПа |
Заключение
В данной статье подчеркивается полезность наномеханического режима PinPoint от компании Park Systems для изучения механических свойств дефектов, чтобы определить, был ли дефект поверхности создан до или после нанесения на нее покрытия. Путем измерения энергии адгезии и разностей модулей упругости между стеклом и материалами покрытия было успешно определено начальное время образования дефекта. Атомно-силовые микроскопы можно использовать для широкого спектра применений в лакокрасочной промышленности ввиду его способности тщательно исследовать поверхностные свойства образцов – свойства, не наблюдаемые иным способом при изучении только топографии. Используя наномеханический режим PinPoint, можно исследовать механические свойства на уровне наномасштабов, изучая различия между разными материалами покрытий и методами их нанесения. Такие преимущества повышают ценность атомно-силового микроскопа как значимого инструмента в промышленных отраслях по нанесению покрытий.
Подробные характеристики
сканирующего атомно-силового микроскопа Park NX10
Ссылки
- Akafuah, N. K., Poozesh, S., Salaimeh, A., Patrick, G., Lawler, K., & Saito, K. (2016). Evolution of the automotive body coating process—A review. Coatings, 6(2), 24.
- Benavides, S. (Ed.). (2009). Corrosion control in the aerospace industry. Elsevier.
- Lee, J., Mahendra, S., & Alvarez, P. J. (2010). Nanomaterials in the construction industry: a review of their applications and environmental health and safety considerations. ACS nano, 4(7), 3580-3590.
- Leopold, J., Neugebauer, R., Löffler, M., Schwenck, M., &Hänle, P. (2006). Influence of coating-substrate systems on chip and burr formation in precision manufacturing. Proceedings of the Institution of Mechanical Engineers, Part B: Journal of Engineering Manufacture, 220(4), 499-506.
- Qiu, C., Wang, J., Mao, S., Guo, W., Cheng, S., & Wang, Y. (2010). Preparation of poly (3, 4‐ethylenedioxythiophene)/poly (styrene sulfonate)(PEDT/PSS) composite and its applications in anti‐static coating. Polymers for Advanced Technologies, 21(9), 651-655.
- Ciacotich, N., Din, R. U., Sloth, J. J., Møller, P., & Gram, L. (2018). An electroplated copper–silver alloy as antibacterial coating on stainless steel. Surface and Coatings Technology, 345, 96-104.
- Kim, C. G., Nam, Y. W., & Choi, J. H. (2018). U.S. Patent Application No. 15/809,345.
- Future Markets. “Automotive.” Nanocoatings. Nov. 2013.
- Carpick, R. W., & Salmeron, M. (1997). Scratching the surface: fundamental investigations of tribology with atomic force microscopy. Chemical reviews, 97(4), 1163-1194.
- Butt, H. J., Cappella, B., &Kappl, M. (2005). Force measurements with the atomic force microscope: Technique, interpretation and applications. Surface science reports, 59(1-6), 1-152.
- John Paul Pineda, Gerald Pascual, Byong Kim, and Keibock Lee (2017). Using AFM PinPoint™ Nanomechanical Mode for Quantification of Elastic Modulus in Materials Two Orders of Magnitude Faster than Force Volume Spectroscopy, Park Systems Application note #26.